In the printing work of the offset printing press, it is often encountered that the circuit controller breaks or breaks due to the failure of the double-sheet circuit controller, the double-sided control slide arm loses oil and causes the operation to malfunction, or the operator Forgot to open the double-sheet control button. At the moment, if the sheet feeder is poorly divided, there will be more than one sheet of paper input, and it will be conveyed into the impression cylinder without blocking, resulting in the occurrence of a roller collision accident.
If the amount of rolled paper is small and the total thickness is not more than 0.8mm, it is possible to take out the paper by turning the cart or by reducing the pressure. However, if the thickness is greater than 0.8 to 1.0 mm, these two methods often do not help.
In the case where the machine is crushed by rolled paper, the following methods are usually used to remove the pressure between the blanket cylinder and the impression cylinder:
1. Sawing and cutting method: Using a hacksaw to start sawing from one end of the blanket cylinder and the impression cylinder to the other end, remove the rubber, nylon cloth and backing paper together to achieve the purpose of releasing the cylinder.
Note: Although this method is easy to operate, but the loss is greater, the risk is also large, and some carelessness, it will scratch the upper and lower two rollers smooth surface, severe can cause scrapping scrap. At the same time, the total price of damaged blankets and nylon cloth is more than 500 yuan. If it is imported materials, the price of blankets will be higher and the losses will be even greater.
2. Impact method: Use two sledgehammers, two round steels of 600mm long and 30mm in diameter. At the same time, impact the end of the equidistant plane of the eccentric sleeve of the rubber roller on the drive side and the operation side (commonly known as the sleeve ears), and force the rotation of the sleeve. Reduce the pressure and remove the paper.
When this method is used, some parts need to be removed (the main part is on the transmission side), which takes a long time. Moreover, the impacted parts are damaged due to the cast iron texture of the material, and their strength is greatly reduced. At the same time, the risk factors for recurrence of the fracture accident are also hidden.
3. Dismantling method: Remove the connecting rods and other connecting parts on the eccentric sleeve (operating surface) of the blanket cylinder, and use the three M8 thread heads on the disc holder to screw in the three thread teams on the sleeve end face. Pull out the sleeve to achieve the purpose of releasing the roller.
Description: This method is relatively simple to operate, but when the rolled paper is thick and the extrusion force is relatively large, the pull sleeve can be easily pulled to make the thread hole slip and cause failure. Since the axial ends of the blanket cylinder are subjected to pressure at the same time, if the sleeve can be pulled out, then when the sleeve is disengaged from the support of the shaft head, the pressure will suddenly be released and suddenly burst into an impact force. The force is far greater than the bending strength of the rubber roller shaft head, so this method can easily cause the roller shaft diameter bending deformation, and make it scrapped.
In summary, due to the frequent occurrence of paper jams, it is time-consuming and labor-intensive to remove them. Generally, it takes 6 to 8 hours. When it is not successful, 2 shifts are required before it can be put back into production. The matching accuracy will be affected, which will also result in a decrease in quality. Therefore, the only thing that has to be changed from printing precision products to printing ordinary products is also common. At the same time, it also speeds up the overhaul period of the aircraft.
From this point of view, in the face of rolling paper failure, which method to use for exclusion, the accuracy of the shutdown, printing quality and production of important factors. I think only by finding a highly efficient, safe and rapid method can we achieve these three technical requirements.
From the arrangement of the three rollers of the offset press, the plate cylinder and the impression cylinder receive only one-way force from the blanket cylinder, and the blanket cylinder bears the upper plate cylinder at the same time. In both directions of force of the drum, when the paper is pressed between the impression cylinder and the blanket cylinder, its pressure will increase abnormally, and the pressure between the blanket cylinder and the plate cylinder is still a normal value. I think that since there is a normal pressure between them, then the plate cylinder is depressurized by a normal pressure regulator until it comes out of contact with the blanket cylinder. This reduces the pressure relative to the blanket cylinder by half. The separation of the nuclear skin roller and the impression cylinder may be easier and the speed will be faster.
According to this idea, in the past two years, it has repeatedly eliminated the use of rolled paper, so it has been constantly groping and summarizing. It has finally overcome one difficulty after another, and it has found a new method that is fast, efficient, and easy and safe.
It takes 6 to 12 hours or more to eliminate faults from the old methods in the past, shortening it to 30 to 90 minutes, and ensuring that all parts of the machine are in good condition without removing a single screw or part.
The following example illustrates the method and process of this method:
June 1995, J2205 machine, Beijing People's Machine Factory production, the machine printing products: natural textbooks, 80g of paper used glue, speed 6000 India / h, rolling time: 9:40 am, rolling paper: 29, The reason for jamming the machine after entering the drum: There is no double detector.
Exclusion method and adjustment order:
1. Open both sides of the shield. Check gears, connecting rods and other parts for damage.
2. In the left and right sides of the four pressure regulators "0" position with yellow ink strokes positioned on the dial, in order to prepare for the reset.
3. Take a copper rod with a diameter of 30mm, a length of 400mm, a hammer of 1.5lb and a socket wrench of 14th (sets). Two people use a 14# socket wrench to rotate the regulators on both sides of the plate cylinder to the “-†direction, and pay attention to the synchronous rotation until the two rollers come out of contact with the nuclear skin rollers. At the same time, record the number of rotations. Down.
4. Simultaneously with both sides of the hand hammer, the copper rod hits and vibrates along the edge of the blanket cylinder, and at the same time uses a No. 14 socket wrench to rotate the blanket cylinder pressure regulator to the “-†direction. The rotation factor should also be recorded.
Pay attention to the operation, the handle of the socket wrench should not be lengthened again, so as not to damage the fan-shaped teeth and the rocker arm, and only press down with the weight, and it is not necessary to loosen. The key factor is the strength of hitting the plate around the outer sleeve (not the eccentric sleeve). If the paper is rolled more; thicker, of course, the strength of the striker plate should be strengthened, and vice versa. In short, the two sides strike as far as possible to keep pace, need to be progressive, with the pressure reducer rotation, the two rollers gradually reduce the pressure, quickly make the blanket cylinder and the impression cylinder out of contact, remove the pressed paper, remove the paper rolling work carry out.
5. Hand crank for 2 weeks, pay attention to whether there is abnormal sound when the machine rotates, and there is no obstacle in the process of automatic pressure separation. Is it heavy?
6. Loosen the blanket so that it has no tension. Apply a layer of “rubber reductant†along the pressure line surface of the blanket that has been squeezed. Wait 3 to 5 minutes before tightening. The tightening force is slightly smaller than before the squeeze, to ensure that the blanket recovers its good elasticity.
7. The two sides of the pressure regulator in accordance with the first reset rubber roll, and then reset the version of the state of the roller state. Take out the record of the number of weeks that the original "-" was turned to, and turn the same number of weeks to "+" to reach the original position. It should be noted that when the regulator is rotated at both ends of a roller, it must be performed synchronously. It is not allowed to start one head at a slow speed to ensure that the accuracy of the matching between the roller shaft and the bushing is not affected.
8. Move the machine a few times to confirm that there is no error, start the operation and proofing, check the product rules, outlets and patterns, if no change, start production.
The above examples were conducted under more skilled conditions, and it took only 40 minutes from the stuck machine to the start of production. At the beginning of the operation, it was also unfamiliar. After mastering this "8" point program, it was carried out in sequence. The speed will be gradually increased and the operation will be more skilled.
The new method developed by itself has increased the production efficiency, ensured the product quality and maintained the equipment, and produced certain economic benefits. This method is also applicable to monochrome machines, two-color machines, and four-color machines. We are willing to make exchanges with our counterparts here to make our printing business even better and contribute to building a socialist enterprise with Chinese characteristics.
Special Purpose
Bags:
Special Purpose
Bags are functional bags, for example, School Bags , Cosmetic Bags, Shopping
Bags, Fireproof Bags, Laptop Bags , Wallets , Cooler Bags, Tool Bags , Stationery Pouches,
Adult Sleeping Bags, Laundry Bags, Camera Bags, Medical Bags, Gift Bags and so
on.
These
bags appear on everywhere, mainly for carrying or
protecting. The bags` look also symbolize an aesthetic standard in an era.
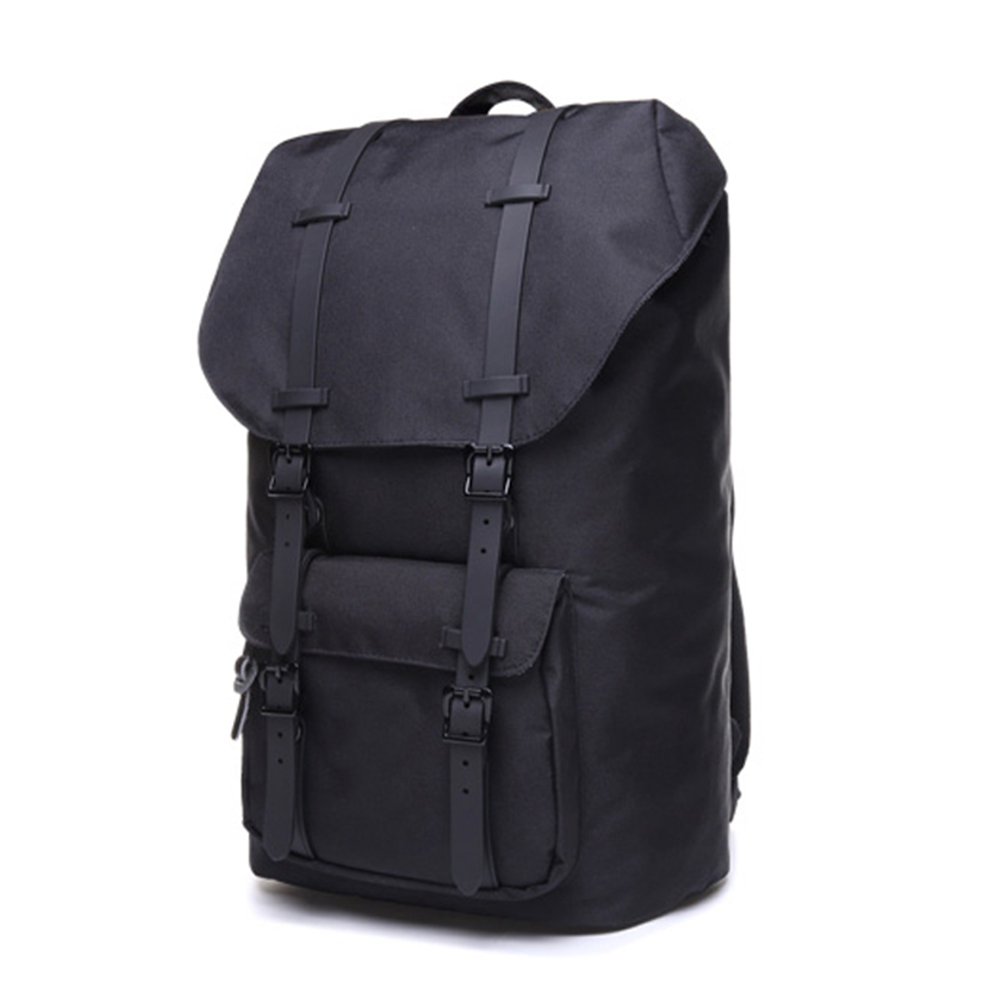
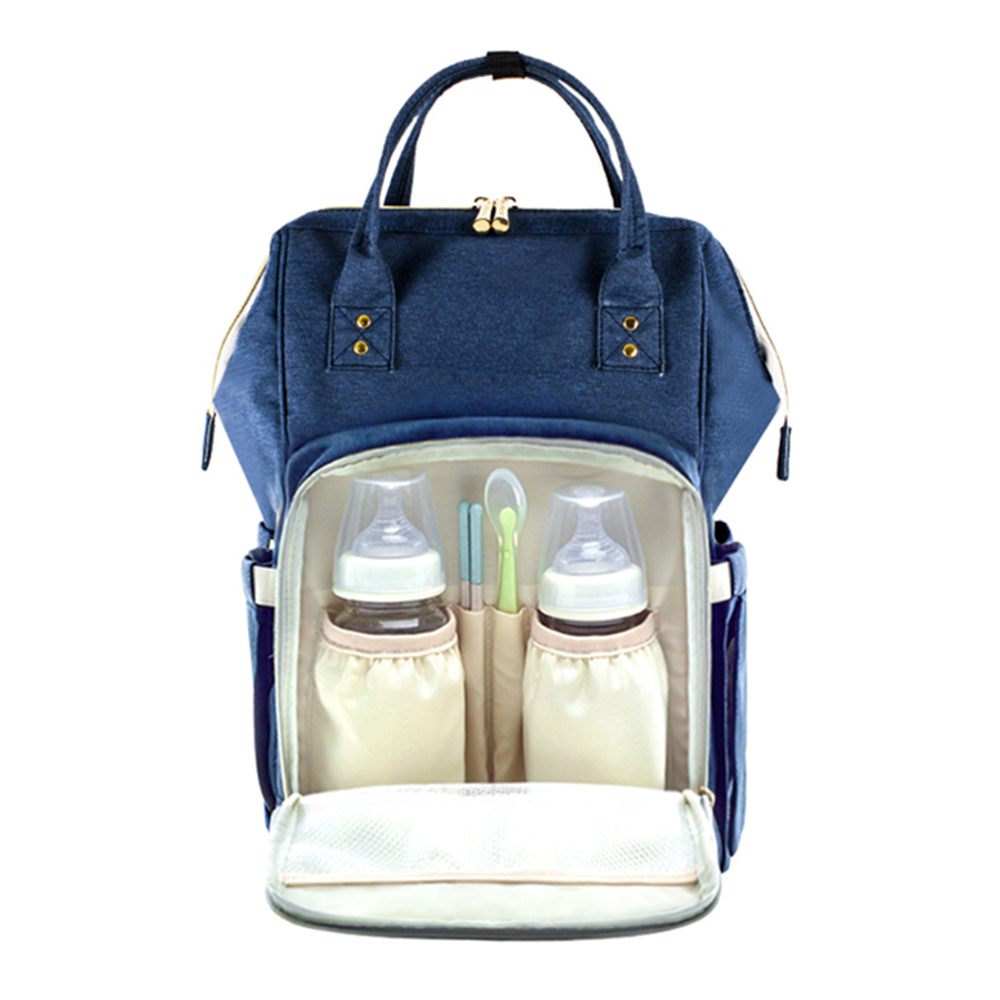
Bags
become more and more commercialized, many designers create fantastic items.
Almost bags are in polyester, canvas, PU leather, nylon PVC etc., and some
people also will create new material to fill the market.
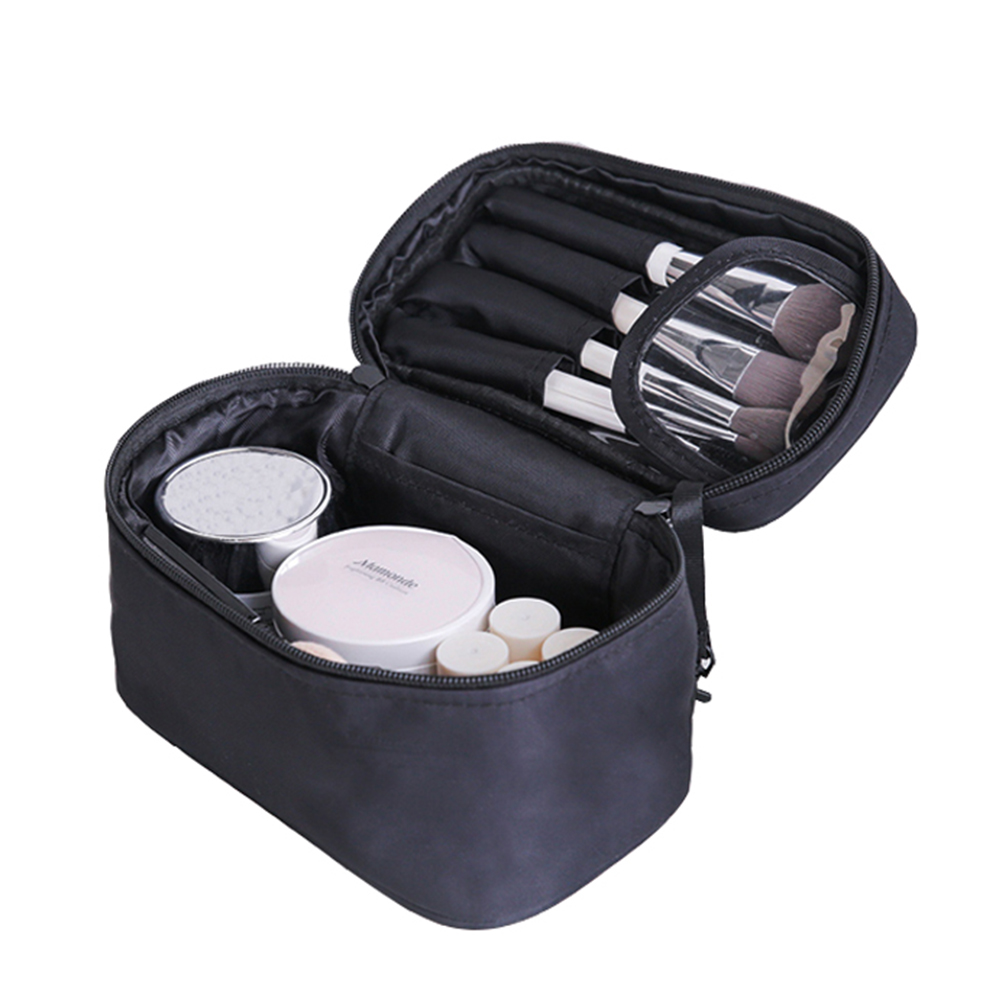
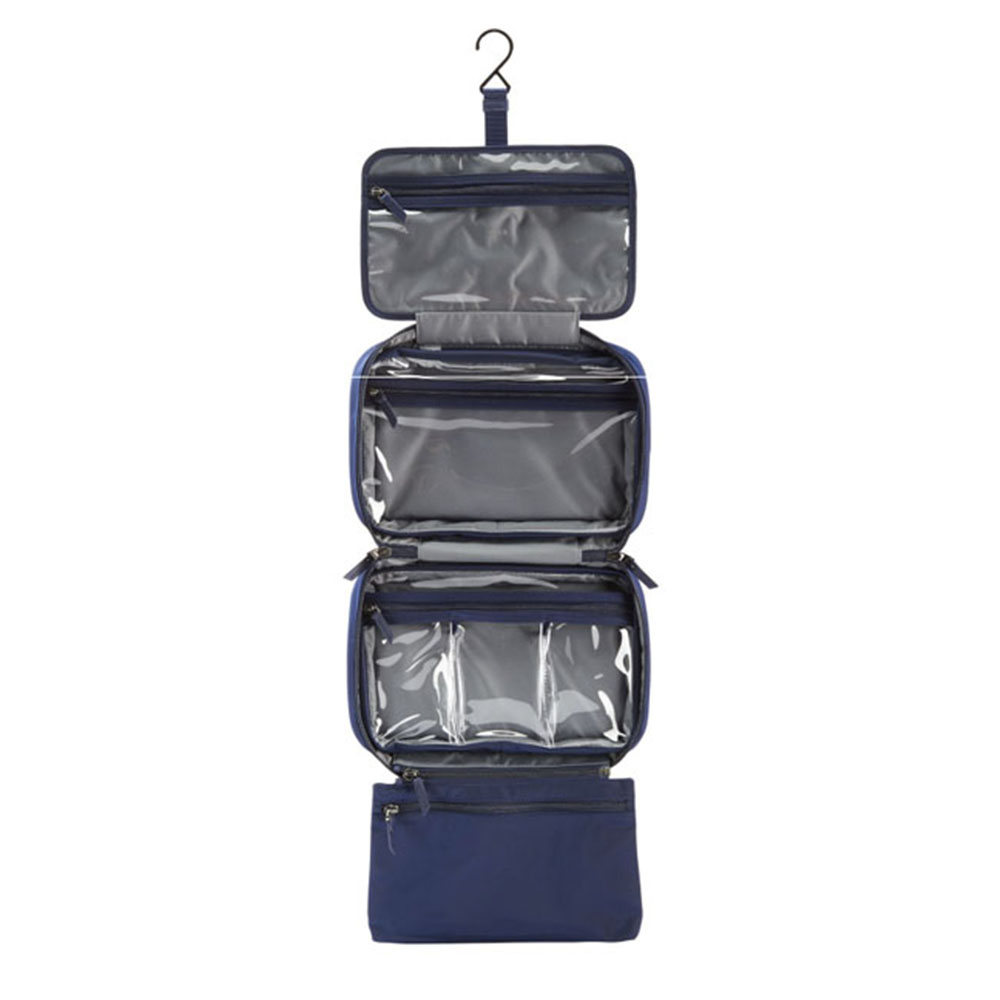
Olinb Bags are a
manufacturer who specialize in making custom bags, attaching a label for
you.
To avoid any bad
feedback about quality from buyers, it is guaranteed that all of our bags
will be well made and 100% checked before delivery. If any issue on
quality, replacement will be sent to you for free.
Olinb Bags' products will give you an edge
over your competitors.
Special Purpose Bags
Special Purpose Bags,Fashion Special Purpose Bag,Special Purpose Bags Cosmetic Bag,Ziplock Special Purpose Bags
Shenzhen Olinb Bags Co., Ltd. , http://www.szolinbbags.com