5.6 Machine Commissioning
The purpose of the machine commissioning is to make the assembled machine in normal working condition, and it is also a comprehensive inspection of machine processing and installation accuracy. A good tuner can find out the problems of the machine through the tuning process, and at the same time reduce the possible harm to the minimum. The tuning process must be careful, and each step must be strictly followed in order to avoid accidents.
The following briefly analyzes the tuning process.
1. Make a full inspection of the machine before operation. It is mainly the installation condition of the machine couplings, positioning parts and anti-loosening parts. Whether there are other foreign materials on the machine or not, especially if the foreign matter is caught in the middle of two rollers, the machine will be seriously damaged.
2. Manually turn the car. In front of the hand, all the wheels are currently used by the pinion to drive the movement of the big gear. This kind of labor-saving mechanism is more convenient to use. It was difficult to determine the uniformity of the rotation by using the root to force the gear to rotate.
3. Move. The jog is mainly used to check the working status of the moving parts and circuits of the machine, to see whether the moving parts have interference phenomenon, whether the circuit works like a clutch and press mechanism, and it is possible to use a hand-moving and disengaging press mechanism to make the machine pressure or pressure. Check the smoothness of the separation.
Other control mechanisms can be manually checked in the case of jogging, such as movement of the transfer roller, transfer roller, and interlocking mechanism. Another important role of jogging is to check the transfer of paper on the driveline. Enter a piece of paper from the front gauge, and use jog to observe its status and movement at any point. If you find that the handover is not good, you can adjust it in time. Therefore, check the jog in both directions. Some parts do not interfere with each other on the right point, and opposing points may interfere with each other. Another important role of jogging is to check the bouncing and skewing of the rotating parts.
4. Slow long car. Make the machine slow and long, so that you can observe the working conditions of various parts of the machine in more cycles.
5. The empty car runs at low speed. The low-speed operation of the empty vehicle refers to the operation at the lowest speed when the machine is working normally. It is mainly used to check the working condition of the oil circuit. If any problem has to be eliminated in time, the moving parts can be further observed to see if there is Abnormal phenomena exist, such as abnormal sounds. After stopping for a period of time, use the manual moving parts to see the connection, positioning and locking.
6. The empty car runs at high speed. The high-speed operation of the empty car is mainly to check the stable operation of the machine and the working condition of the bearing. Some features of the machine do not show up at low speeds, and a pair of high speeds may show up as their inertia and impact increase.
7. Empty car at low speed. The low-speed paper transport mainly checks the paper transfer status, including whether the gas path work is abnormal or not, and whether the coordination at each interface is accurate, and if it is found inappropriate, it should be adjusted in time. It should be noted that several types of paper should be used when moving paper, so that some hidden problems can be exposed.
8. Empty high speed paper. The high-speed travel of the empty car mainly checks the stability of its paper feeding, and at the same time, it can also check the working condition of the gas line at high speed.
9. Let me run at a low speed. After the machine's water and ink paths are installed, installing the printing plate at a low speed mainly involves the influence of printing pressure on the operation of the machine. The inertial impact caused by the printing pressure may increase the vibration of the machine.
10. Load Wujian Tongluo. This step is to further check the stability of the machine load operation, which is very important. From a machine perspective, the machine should be in good working condition within the specified speed range.
11. Overprint accuracy testing. Accuracy of overprinting is one of the most important indicators to measure the accuracy of the machine. If the overprinting fails to meet the requirements, the quality of the printed matter will not be discussed. The following analysis of the general method of detection overprint accuracy for reference.
(1) Simultaneous speed detection At the same speed, the printed paper is placed on the paper transport pile at the same speed, and the printing process is repeated. Take a look at whether the size of the two overprint errors is within the specified range. This is the method used for general equipment requirements.
(2) Allometry detection Allometry detection is the printing of a printed sheet at another speed and printing at another speed, and see if the size of the overlay error at different speeds meets the requirements. Precision equipment requires this method.
(3) Variable speed detection. Variable speed testing is to make the machine in the printing process from low speed to high speed, and then change from high speed to low speed, and then print the printed sheet again and again, while the speed is still changing, look at the misprinting of Figure 5, 15a difference The size of this detection method is mainly used to detect the stability of the overprint. Except for extremely precise equipment, this method is rarely used. But this method is the most comprehensive.
There are two points to note when registering the accuracy test: First, the rules should be as thin as possible, too thick will affect the test results; second, there should be rules in the front, middle and back parts of the printed sheet, as shown in Figure 5.15. Show. This allows you to check the overprint of the entire layout (in this case, you should consider the effects of the printing process).
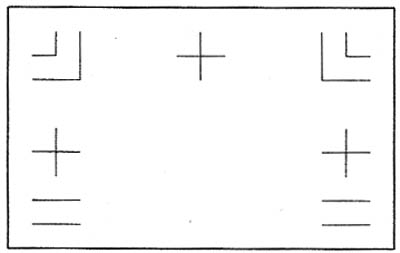
12. Ink uniformity. Ink uniformity is an important indicator of the accuracy of the roller surface processing. Checking the uniformity of the ink color is usually done through the printing plane. This can only be a rough look at the surface. The precise government method is to put some test strips on the entire layout consciously, and check the density values ​​of the corresponding color patches on the test strip. The values ​​measured on each block are compared together, and the difference between the maximum value and the minimum value is removed to the average value, and this value should generally be controlled at about 10%. Less than this number can be considered qualified; greater than this number can be considered unqualified. When failing, the reason should be analyzed in detail. If it is the cause of the equipment, it should be negotiated with the factory in time. However, this range is not the same for different machines. It is necessary to determine whether it is qualified according to the technical specifications. Ink uniformity and overprinting are not the same in nature and should not be confused with the two indicators.
13. Expanded value of outlets. At the time of printing, the expanded value of the dot can be detected at the same time. The expanded value of outlets is closely related to the quality of reproduction of printed products. The expansion value of outlets should be based on the smoothness and smoothness of the outlets, and the layout of outlets should be basically the same. This index must be strictly in accordance with technical requirements, otherwise the difference is greater. If you track with a signal strip, you can approximate the expansion value of the dot with a percentage of the density difference of 50% fine net and 50% coarse net, and of course, a more precise algorithm. The expansion value of general outlets should be controlled at less than 15 percent.
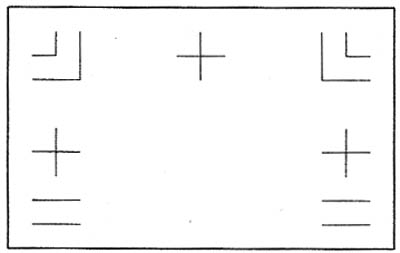
14. Field arbitrage. The density of field density is an important indicator of whether or not the print product level can be reproduced. The greater the density in the field, the richer the level and the stronger the ability to reproduce the manuscript. The density of solids should be based on the average of the entire layout.
15. The machine runs smoothly (consistent print quality). After the machine is in normal operation, print a sufficient number of products to see how much the quality changes before and after the machine. If it is within the scope of the license, it can be considered that its stability meets the requirements; otherwise, it must be carefully analyzed and the reason for re-testing.
16. Noise. Machine noise measurements can be made with reference to technical requirements. Generally, the sound level meter is placed one meter away from the measured location, and the height of 1.5 meters. The noise of the whole machine is based on the average value of each part shown in Figure 5.16. In the section of machine layout, the utilization of various aspects of the machine has been analyzed in detail. In practice, the size of the noise should be a weighted average, and the results obtained are more in line with the actual situation. The size of the machine noise is closely related to the surrounding environment and the low noise. When the noise drives out the indicator (>85db(A)), the cause of the noise should be analyzed in detail and controlled.
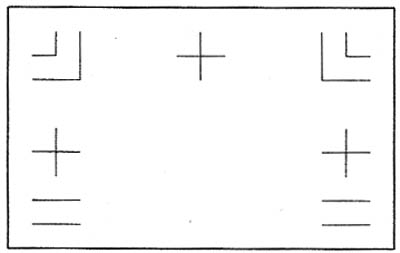
17. Temperature rise. Temperature rise is an important indicator for checking the working conditions of bearings. The higher the temperature rise, the more difficult it is for the oil film to form and the bearing wear to increase. One of the main heat sources for the machine is the air pump. The temperature rise (<65°C) of the air pump must also be strictly controlled.